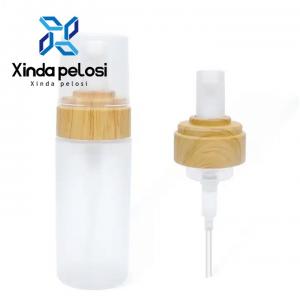
Add to Cart
item | value |
Surface Handling | Frost |
Industrial Use | Personal Care |
Sealing Type | PUMP SPRAYER |
Use | Skin Care Cream |
Place of Origin | China |
Fujian | |
Usage | Skin Care Cosmetic Packaging |
Color | Frosted glass, amber,dark green |
Material | Glass + bamboo |
Capacity | 30g 50g 100g 120g |
Volume | 30ml/50ml/100ml/120ml |
Cap | Eco-friendly bamboo cap |
Shape | Round |
Feature | Eco-friendly sustainable organic |
Certification | Food and Drug Administration |
Introduction (H1)
The creation of high-quality lotion dispenser pumps involves a meticulous manufacturing process that balances precision and efficiency. In this exploration, we'll unravel the techniques employed to produce these essential components, shedding light on the intricacies that contribute to their functionality.
Material Selection (H2)
Plastic Resins (H3)
Lotion dispenser pumps are predominantly crafted from plastic resins. The selection of the appropriate resin depends on factors such as durability, chemical resistance, and aesthetic requirements. Common choices include polypropylene (PP) and polyethylene (PE) for their robust properties.
Metal Components (H3)
Certain components, like the pump mechanism, may incorporate metal elements such as stainless steel. Stainless steel ensures longevity and corrosion resistance, vital for components in direct contact with the lotion.
Injection Molding (H2)
Tooling Design (H3)
The heart of lotion dispenser pump manufacturing lies in injection molding. Precise tooling design is crucial to creating the intricate shapes and structures of the pump components. Computer-Aided Design (CAD) plays a pivotal role in crafting molds that mirror the desired specifications.
Melted Precision (H3)
During injection molding, plastic resin is heated to a molten state and injected into the meticulously designed molds. This process allows for the creation of intricate parts with consistency, ensuring each lotion dispenser pump meets the required standards.
Assembly Processes (H2)
Automated Assembly (H3)
The assembly of lotion dispenser pumps often involves automated processes to ensure efficiency and consistency. Automated assembly lines are programmed to piece together the various components, including the pump, collar, and dip tube, with precision.
Quality Checks (H3)
At each stage of assembly, rigorous quality checks are implemented to guarantee that each lotion dispenser pump meets the predefined standards. This includes functional tests to ensure the pump dispenses the correct dosage and visual inspections to detect any defects.
Surface Finishing (H2)
Decorative Coating (H3)
To enhance aesthetics and brand representation, lotion dispenser pumps may undergo decorative coating processes. This can include metallic finishes, matte textures, or custom colors to align with the branding of the product.
Printing and Labeling (H3)
Branding elements and essential information are added through printing or labeling. This step ensures that the lotion dispenser pumps not only function flawlessly but also serve as a visually appealing part of the product.
Quality Assurance (H2)
Random Sampling (H3)
Quality assurance extends beyond the assembly line. Random sampling of finished lotion dispenser pumps is conducted, subjecting them to various tests to verify durability, functionality, and adherence to design specifications.
Adherence to Regulations (H3)
Stringent adherence to regulatory standards is paramount. Lotion dispenser pumps must comply with industry regulations to guarantee user safety and satisfaction.
Conclusion (H1)
In conclusion, the manufacturing of lotion dispenser pumps involves a sophisticated interplay of material science, precision engineering, and quality assurance. By embracing these techniques, manufacturers ensure that each pump delivers not just lotion but an experience of reliability and functionality.
Why is injection molding the preferred method for manufacturing lotion dispenser pumps?
Injection molding allows for the creation of intricate shapes with consistency, ensuring each pump meets the required standards efficiently.
What materials are commonly used in crafting lotion dispenser pumps?
Plastic resins such as polypropylene (PP) and polyethylene (PE) are commonly used, along with stainless steel for certain components.
How are lotion dispenser pumps assembled?
Automated assembly lines are often employed to piece together various components, with rigorous quality checks at each stage.
Why is surface finishing important for lotion dispenser pumps?
Surface finishing enhances aesthetics and brand representation, making the pumps visually appealing and aligned with the product's branding.
What quality checks are conducted during the manufacturing process?
Quality checks include functional tests to ensure correct dosage dispensing, visual inspections for defects, and random sampling for durability and adherence to specifications.